Casting processing is a process in which molten metal liquid that meets the requirements is poured into a specific casting mold, and the desired shape, size, and performance are obtained after cooling and solidification. It is widely used in aerospace, automobile, machine tool manufacturing and other industries because of its excellent characteristics such as easy molding, low cost, and less time consumption.
Casting technology in our country is not a new technology, but a cultural heritage with a long history. However, the current traditional casting process has been unable to meet the modern needs for casting products in terms of design quality and design concepts. Therefore, how to create new casting process technology requires in-depth discussion and research. Compared with other processing and forming methods, the precision of the casting process is poor, and the structural properties are not as good as forging. Therefore, how to improve the accuracy of castings and optimize their structural properties is also worthy of attention and research.
The material for the mold can be sand, metal or even ceramic. Depending on the requirements, the methods used will vary. What are the characteristics of each casting process? What kind of products are suitable for it?
1. Sand casting
Casting material: various materials
Casting quality: tens of grams - tens of tons to hundreds of tons
Casting surface quality: poor
Casting structure: simple
Production cost: low
Scope of application: The most commonly used casting methods. Hand molding is suitable for single pieces, small batches and large castings with complex shapes that are difficult to use a molding machine. Machine modeling is suitable for medium and small castings produced in batches.
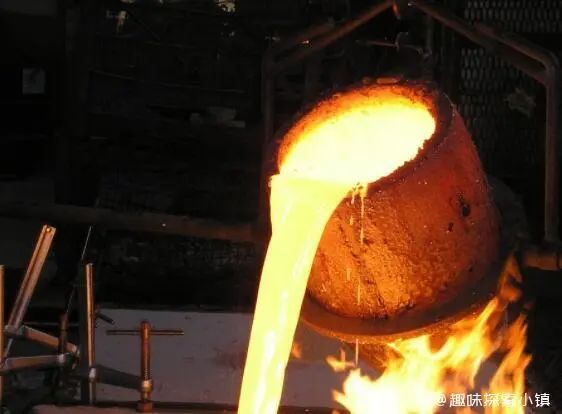
Process characteristics: Manual modeling: flexible and easy, but has low production efficiency, high labor intensity, and low dimensional accuracy and surface quality. Machine modeling: high dimensional accuracy and surface quality, but high investment.
Sand casting is the most commonly used casting process in the foundry industry today. It is suitable for various materials. Ferrous alloys and non-ferrous alloys can be cast with sand molds. It can produce castings ranging from tens of grams to tens of tons and larger. The disadvantage of sand casting is that it can only produce castings with relatively simple structures. The biggest advantage of sand casting is: low production cost. However, in terms of surface finish, casting metallography, and internal density, it is relatively low. In terms of modeling, it can be hand-shaped or machine-shaped. Hand molding is suitable for single pieces, small batches and large castings with complex shapes that are difficult to use a molding machine. Machine modeling can greatly improve surface accuracy and dimensional accuracy, but the investment is relatively large.
2. Investment casting
Casting material: cast steel and non-ferrous alloy
Casting quality: several grams---several kilograms
Casting surface quality: very good
Casting structure: any complexity
Production cost: In mass production, it is cheaper than completely machining production.
Scope of application: Various batches of small and complex precision castings of cast steel and high melting point alloys, especially suitable for casting artworks and precision mechanical parts.
Process characteristics: dimensional accuracy, smooth surface, but low production efficiency.
The investment casting process originated earlier. In my country, the investment casting process has been used in the production of jewelry for nobles during the Spring and Autumn Period. Investment castings are generally more complex and are not suitable for large castings. The process is complex and difficult to control, and the materials used and consumed are relatively expensive. Therefore, it is suitable for the production of small parts with complex shapes, high precision requirements, or difficult to perform other processing, such as turbine engine blades.
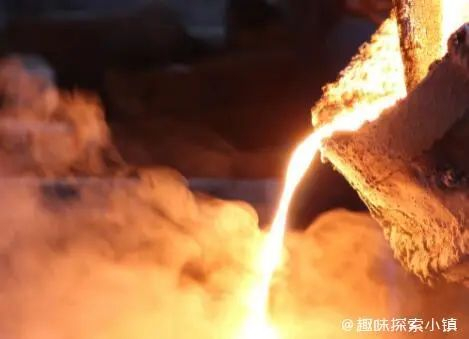
3. Lost foam casting
Casting material: various materials
Casting mass: several grams to several tons
Casting surface quality: good
Casting structure: more complex
Production cost: lower
Scope of application: more complex and various alloy castings in different batches.
Process characteristics: The dimensional accuracy of the castings is high, the casting design freedom is large, and the process is simple, but the pattern combustion has certain environmental impact.
Lost foam casting is to bond and combine paraffin or foam models similar in size and shape to the castings into model clusters. After brushing with refractory paint and drying, they are buried in dry quartz sand and vibrated to shape, and poured under negative pressure to vaporize the model. , a new casting method in which liquid metal occupies the position of the model and solidifies and cools to form a casting. Lost foam casting is a new process with almost no margin and accurate molding. This process does not require mold taking, no parting surface, and no sand core. Therefore, the casting has no flash, burrs and draft slope, and reduces the cost of mold cores. Dimensional errors caused by combination.
The above eleven casting methods have different process characteristics. In casting production, corresponding casting methods should be selected for different castings. In fact, it is difficult to say that the difficult-to-grow casting process has absolute advantages. In production, everyone also chooses the applicable process and the process method with lower cost performance.
4. Centrifugal casting
Casting material: gray cast iron, ductile iron
Casting quality: tens of kilograms to several tons
Casting surface quality: good
Casting structure: generally cylindrical castings
Production cost: lower
Scope of application: small to large batches of rotating body castings and pipe fittings of various diameters.
Process features: Castings have high dimensional accuracy, smooth surface, dense structure, and high production efficiency.
Centrifugal casting refers to a casting method in which liquid metal is poured into a rotating mold, filled and solidified into a casting under the action of centrifugal force. The machine used for centrifugal casting is called centrifugal casting machine.
The first patent for centrifugal casting was proposed by the British Erchardt in 1809. It was not until the early twentieth century that this method was gradually adopted in production. In the 1930s, our country also began to use centrifugal tubes and cylinder castings such as iron pipes, copper sleeves, cylinder liners, bimetallic steel-backed copper sleeves, etc. Centrifugal casting is almost a major method; in addition, in heat-resistant steel rollers , some special steel seamless tube blanks, paper machine drying drums and other production areas, the centrifugal casting method is also used very effectively. At present, a highly mechanized and automated centrifugal casting machine has been produced, and a mass-produced mechanized centrifugal pipe casting workshop has been built.
5. Low pressure casting
Casting material: non-ferrous alloy
Casting quality: tens of grams to tens of kilograms
Casting surface quality: good
Casting structure: complex (sand core available)
Production cost: The production cost of metal type is high
Scope of application: small batches, preferably large batches of large and medium-sized non-ferrous alloy castings, and can produce thin-walled castings.
Process characteristics: The casting structure is dense, the process yield is high, the equipment is relatively simple, and various casting molds can be used, but the productivity is relatively low.
Low-pressure casting is a casting method in which liquid metal fills the mold and solidifies into a casting under the action of low-pressure gas. Low-pressure casting was initially mainly used for the production of aluminum alloy castings, and later its use was further expanded to produce copper castings, iron castings and steel castings with high melting points.
6. Pressure casting
Casting material: aluminum alloy, magnesium alloy
Casting quality: several grams to tens of kilograms
Casting surface quality: good
Casting structure: complex (sand core available)
Production costs: Die-casting machines and molds are expensive to make
Scope of application: Mass production of various small and medium-sized non-ferrous alloy castings, thin-walled castings, and pressure-resistant castings.
Process characteristics: Castings have high dimensional accuracy, smooth surface, dense structure, high production efficiency, and low cost, but the cost of die-casting machines and molds is high.
Pressure casting has two major characteristics: high-pressure and high-speed filling of die-casting molds. Its commonly used injection specific pressure is from several thousand to tens of thousands of kPa, or even as high as 2×105kPa. The filling speed is about 10-50m/s, and sometimes it can even reach more than 100m/s. The filling time is very short, generally in the range of 0.01-0.2s. Compared with other casting methods, die casting has the following three advantages: good product quality, high dimensional accuracy of castings, generally equivalent to grade 6 to 7, or even up to grade 4; good surface finish, generally equivalent to grade 5 to 8; strength It has higher hardness, and its strength is generally 25~30% higher than that of sand casting, but its elongation is reduced by about 70%; it has stable dimensions and good interchangeability; it can die-cast thin-walled and complex castings. For example, the current minimum wall thickness of zinc alloy die-casting parts can reach 0.3mm; the minimum wall thickness of aluminum alloy castings can reach 0.5mm; the minimum casting hole diameter is 0.7mm; and the minimum thread pitch is 0.75mm.
Post time: Jul-08-2024